Environmental Management
Environmental Policy
We contribute to creating a sustainable society through corporate activities that are in harmony with the global environment.
Guidelines for Action
- ① Toward the realization of a recycling-oriented society, we will promote the effective use of resources and provide products that reduce the environmental impact.
- ② We will comply with laws and regulations related to the global environment and conduct corporate activities that fulfill our social responsibilities.
- ③ We will raise the environmental awareness of all employees and maintain and improve our environmental management system.
Environmental concept "Ec'Coater"
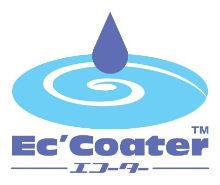
"Ec'Coater" is a word we created that combines the concepts of ecology and a coater. This original concept came from our attitude basing the environment first in our business.
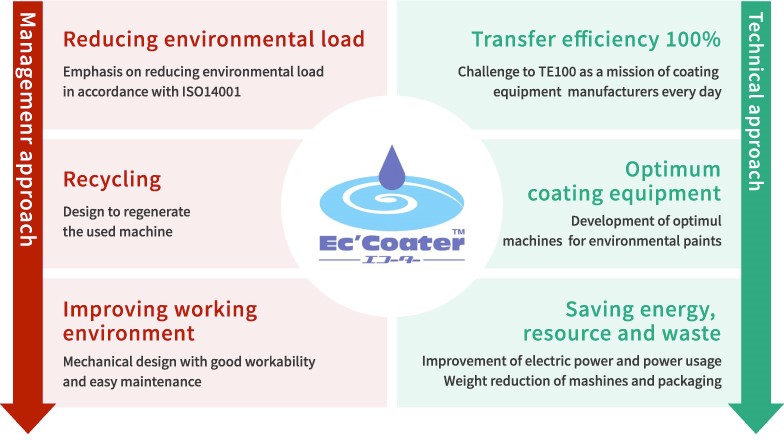
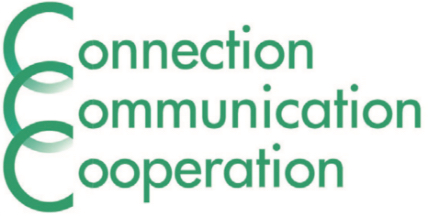
We will continue to challenge solutions by constantly incorporating the most advanced technologies such as IoT and deepening "connection", "communication" and "cooperation" with customers.
Net Shaper
Net Shaper is our original development concept that offers a forging system that aims to reduce secondary processing after forging and improve work environments to reduce total costs through the optimal design of forging processes and tooling and the development of new functions and mechanisms of forging machines.
Product Developments that Reduce Environmental Impact
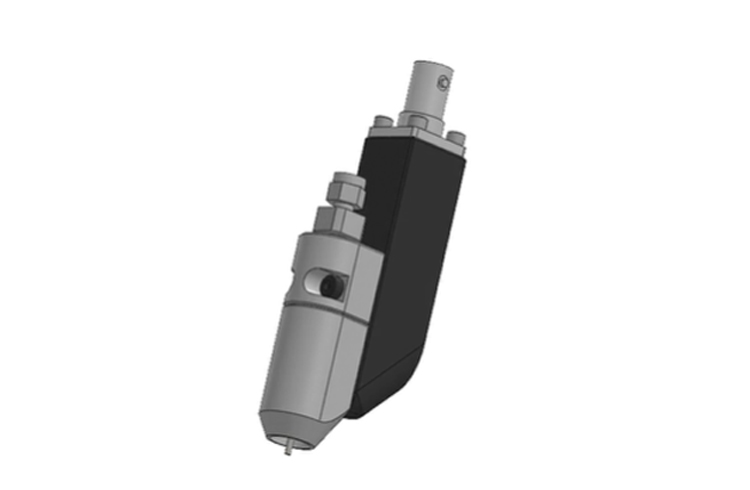
No air is required as the atomization method is based on electrostatic action. This nozzle forms to high precision coating film by high atomizing and micro discharging rate. In addition, since no air is used for atomization, a stable film-forming environment is ensured.
Acquisition of Environmental Management System certification ISO14001
Asahi Sunac Co., Ltd. received the ISO 14001 certification, an international standard for environmental management systems, by the Japan Quality Assurance Organization, a certification body, on February 1, 2002.
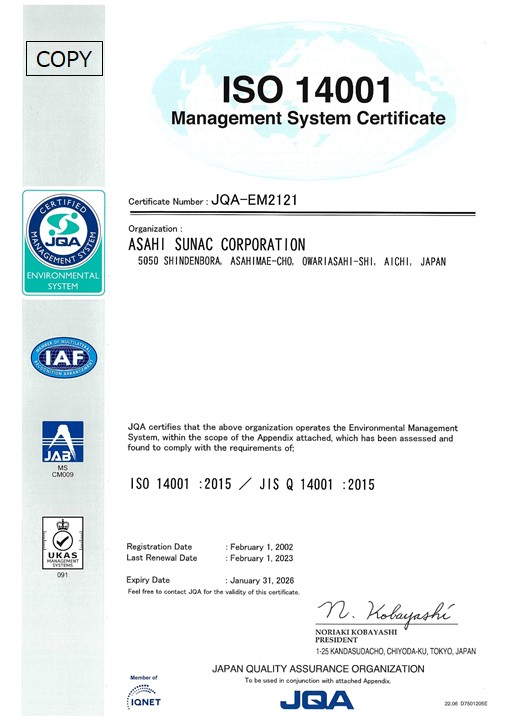
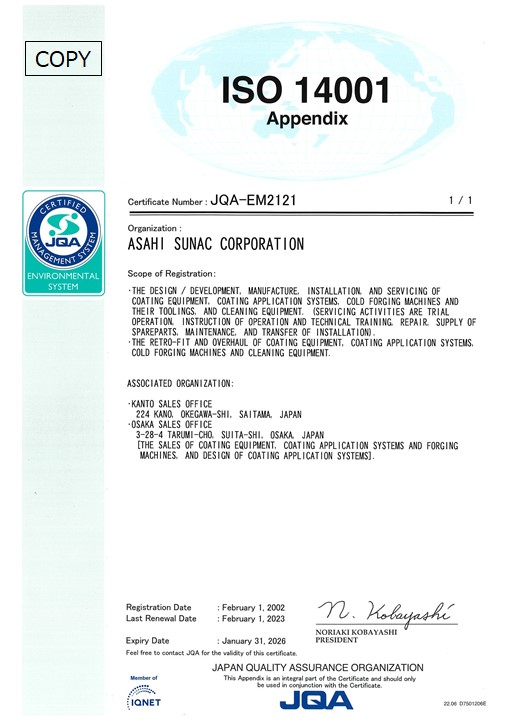
Asahi Sunac complies with the Environmental Management System ISO14001.
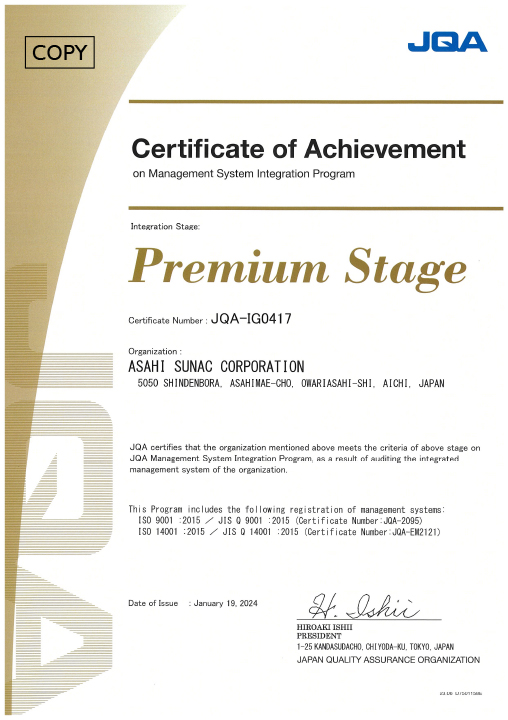
Asahi Sunac has been judged to meet the criteria of the Premium Stage of JQA Management System Integration Program.
Energy Saving Activities
Six activities to significantly reduce carbon dioxide emissions
Approximately 95% of all of our company energy consumption is from electrical power. In order to use our electricity more efficiently, we introduced a power surveillance system in March 2008. This system allows employees to access and view the power consumption of their own and every other division every day, 24 hours a day, and view related graphs, etc., on their computers in real time. Using this data as a resource, each factory and office is able to implement energy saving measures and improve or reduce their consumption. Using these measures, we have been able to significantly reduce levels of carbon dioxide released into the atmosphere and are able to continuously adjust our plans to reduce our environmental impact.
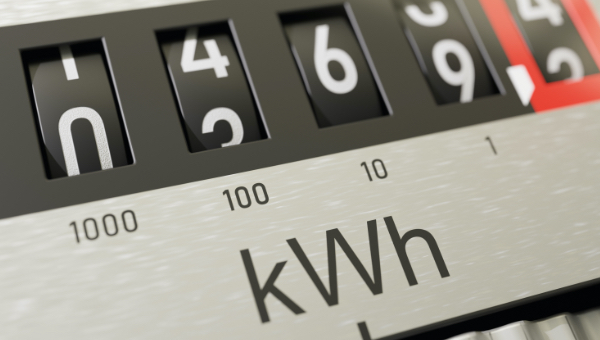
- Power Surveillance System
- Introduced the power surveillance system at 72 locations from March 2003. Monitoring 24 hours in real time.
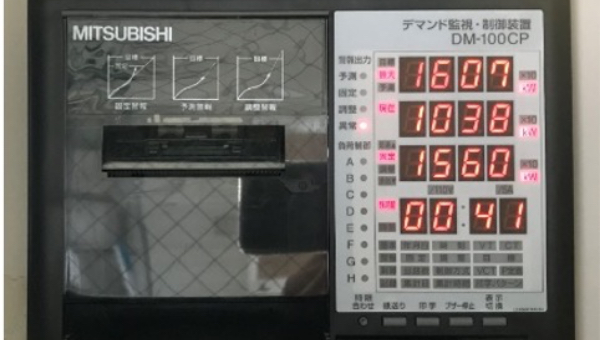
- Demand Monitoring
- The maximum demand power (demand value) is predicted every 30 minutes, and an alarm is triggered when it/the power exceeds the target value to control the power peak. Raise awareness of energy saving in the company to reduce power consumption

- Management of air conditioning
- Temperature setting for air conditioning units are enforced and power during standby mode has been reduced. Heat shield paint has been applied to the rooftops of factories and office buildings, reducing air conditioning power consumption. Older air conditioning models have been replaced and updated with new energy saving units, reducing power consumption.
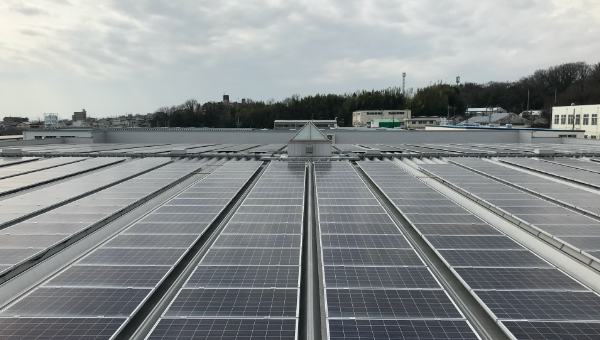
- Solar Power
- 900 solar panels are installed on the roof of the C & F factory to generate 260,000 KWh of electricity annually. At the Kanto sales office, self-consumption solar power generator (80,000 KWh per year) has been installed to reduce CO₂ emission.
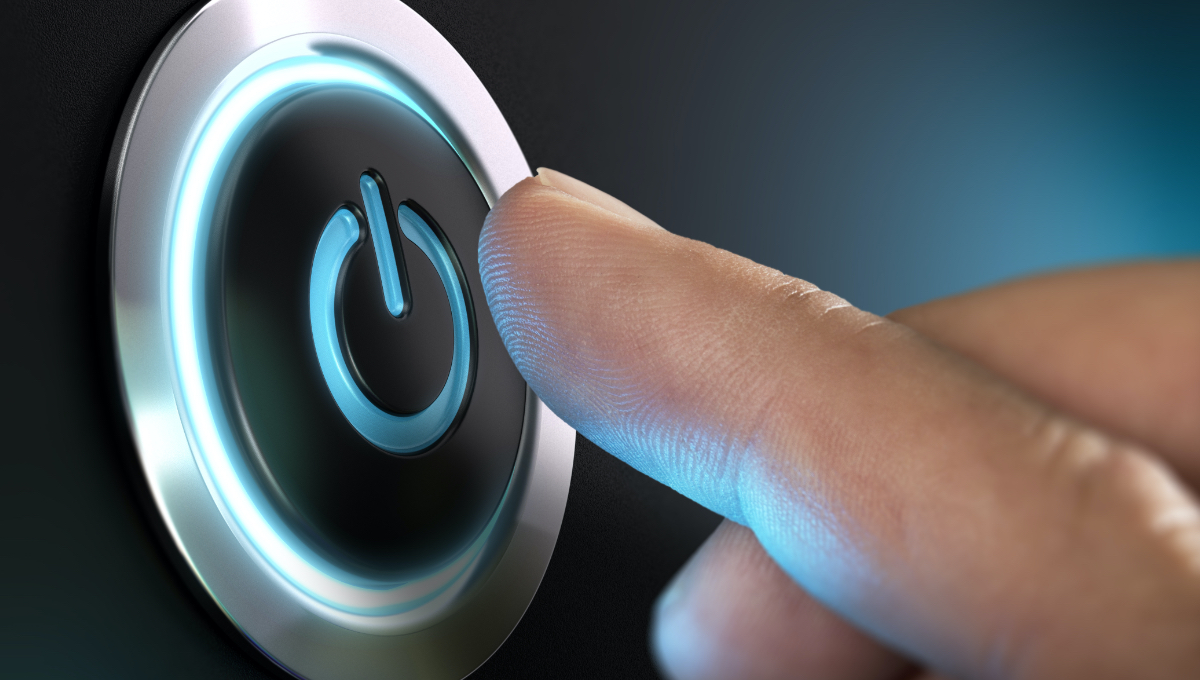
- Management of machine tools
- Each machine tool has been assigned a control manager who is in charge of turning off the main power during scheduled times, reducing power consumed by hydraulic pump units and coolant pumps in standby mode.
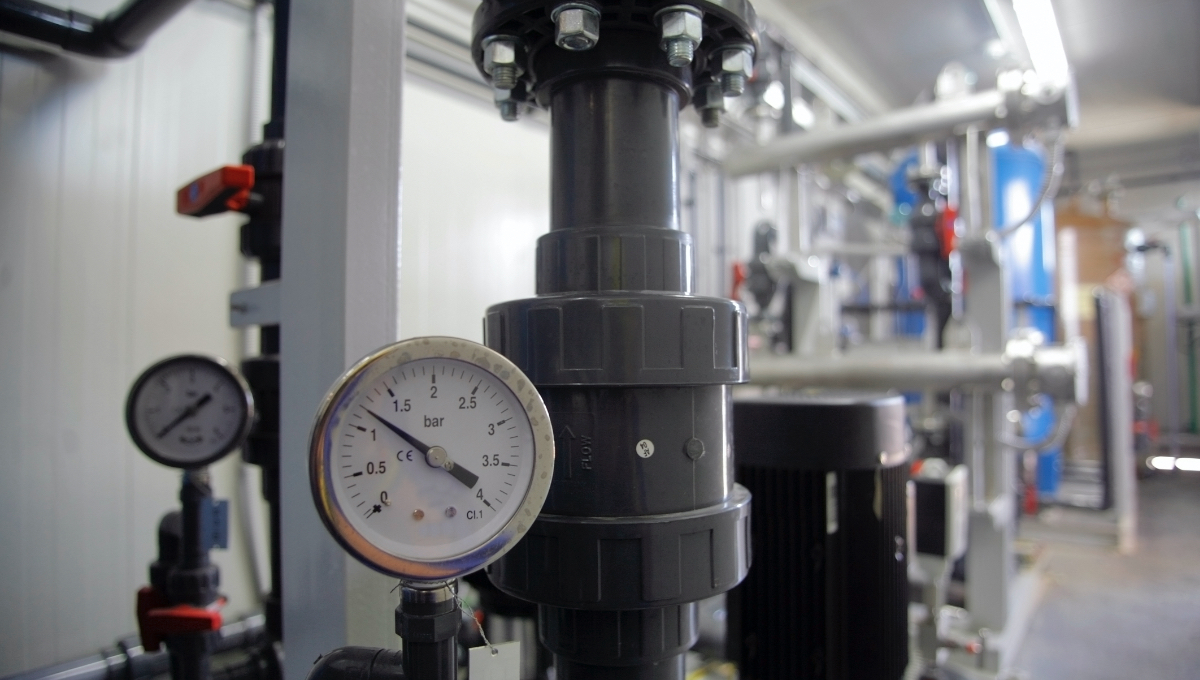
- Management of compressors
- "Energy saving compressor units have been introduced to help reduce power consumption. Compressors are only run during scheduled production to help reduce unwanted usage and power. Air leak sensors are used to check air leaks and help eliminate wasted air usage."